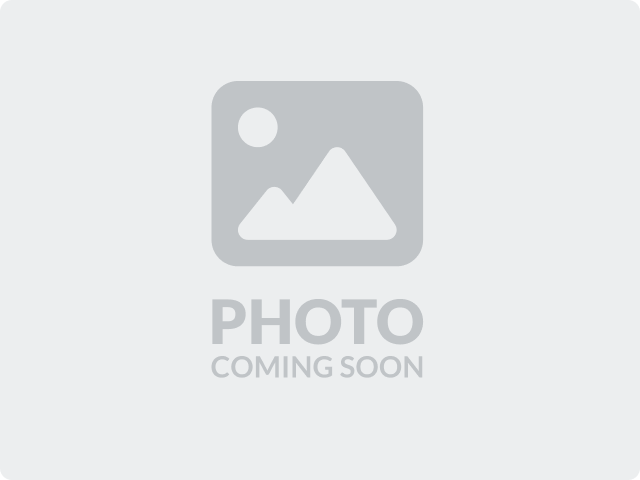
説明
Missing Parts: Main power breaker, Xport Power board, Control PCB, DC Power distribution, Hsisc PC, ASI PC, Turret, Camera & LP board構成
構成なしOEMモデルの説明
The NSX-115 is a model in the NSX Series, which provides fast, repeatable, advanced macro inspection to detect defects created during wafer manufacturing, probing, bumping and dicing or through general handling. The NSX System detects probe marks and generates location and size information and other parameters. The WaferWoRx analysis module converts what has been a manual and time-consuming process of gathering scrub data from various tools, correlating the data, and sifting through for trends, to automated data collection and analysis completed in a single step. It breaks the overall probing error into its core components (prober, probe card, setup), enabling rapid problem resolution. The WaferWoRx probe process analysis capability is available now on the NSX Series and can be ordered as an upgrade for the NSX 100, NSX 105 or NSX 115 models. It also can prequalify test cells without risk to production wafers and evaluate the readiness of the probing process for advanced technologies such as multi-DUT and high pin count probe cards. Probe card performance can be tracked to predict the need for maintenance, thereby extending card life and maximizing card availability. Macro defects (0.5 µm and larger) can have a major impact on the quality of a microelectronic device and on the yield of the manufacturing process. The NSX uses high speed optical microscopy to identify defective probe marks. This same optical characterization data from a well-designed sample of probe marks serves as the input to the WaferWoRx analysis module for processing and further identification of the error components.ドキュメント
ドキュメントなし
ONTO / RUDOLPH / AUGUST
NSX-115
検証済み
カテゴリ
Defect Inspection
最終検証: 60日以上前
主なアイテムの詳細
状態:
Used
稼働ステータス:
不明
製品ID:
60341
ウェーハサイズ:
不明
ヴィンテージ:
2010
Have Additional Questions?
Logistics Support
Available
Money Back Guarantee
Available
Transaction Insured by Moov
Available
Refurbishment Services
Available
同様のリスト
すべて表示ONTO / RUDOLPH / AUGUST
NSX-115
カテゴリ
Defect Inspection
最終検証: 60日以上前
主なアイテムの詳細
状態:
Used
稼働ステータス:
不明
製品ID:
60341
ウェーハサイズ:
不明
ヴィンテージ:
2010
Have Additional Questions?
Logistics Support
Available
Money Back Guarantee
Available
Transaction Insured by Moov
Available
Refurbishment Services
Available
説明
Missing Parts: Main power breaker, Xport Power board, Control PCB, DC Power distribution, Hsisc PC, ASI PC, Turret, Camera & LP board構成
構成なしOEMモデルの説明
The NSX-115 is a model in the NSX Series, which provides fast, repeatable, advanced macro inspection to detect defects created during wafer manufacturing, probing, bumping and dicing or through general handling. The NSX System detects probe marks and generates location and size information and other parameters. The WaferWoRx analysis module converts what has been a manual and time-consuming process of gathering scrub data from various tools, correlating the data, and sifting through for trends, to automated data collection and analysis completed in a single step. It breaks the overall probing error into its core components (prober, probe card, setup), enabling rapid problem resolution. The WaferWoRx probe process analysis capability is available now on the NSX Series and can be ordered as an upgrade for the NSX 100, NSX 105 or NSX 115 models. It also can prequalify test cells without risk to production wafers and evaluate the readiness of the probing process for advanced technologies such as multi-DUT and high pin count probe cards. Probe card performance can be tracked to predict the need for maintenance, thereby extending card life and maximizing card availability. Macro defects (0.5 µm and larger) can have a major impact on the quality of a microelectronic device and on the yield of the manufacturing process. The NSX uses high speed optical microscopy to identify defective probe marks. This same optical characterization data from a well-designed sample of probe marks serves as the input to the WaferWoRx analysis module for processing and further identification of the error components.ドキュメント
ドキュメントなし